A Deep Dive into the Materials Used for Wheel Simulators
Oct 26, 2024
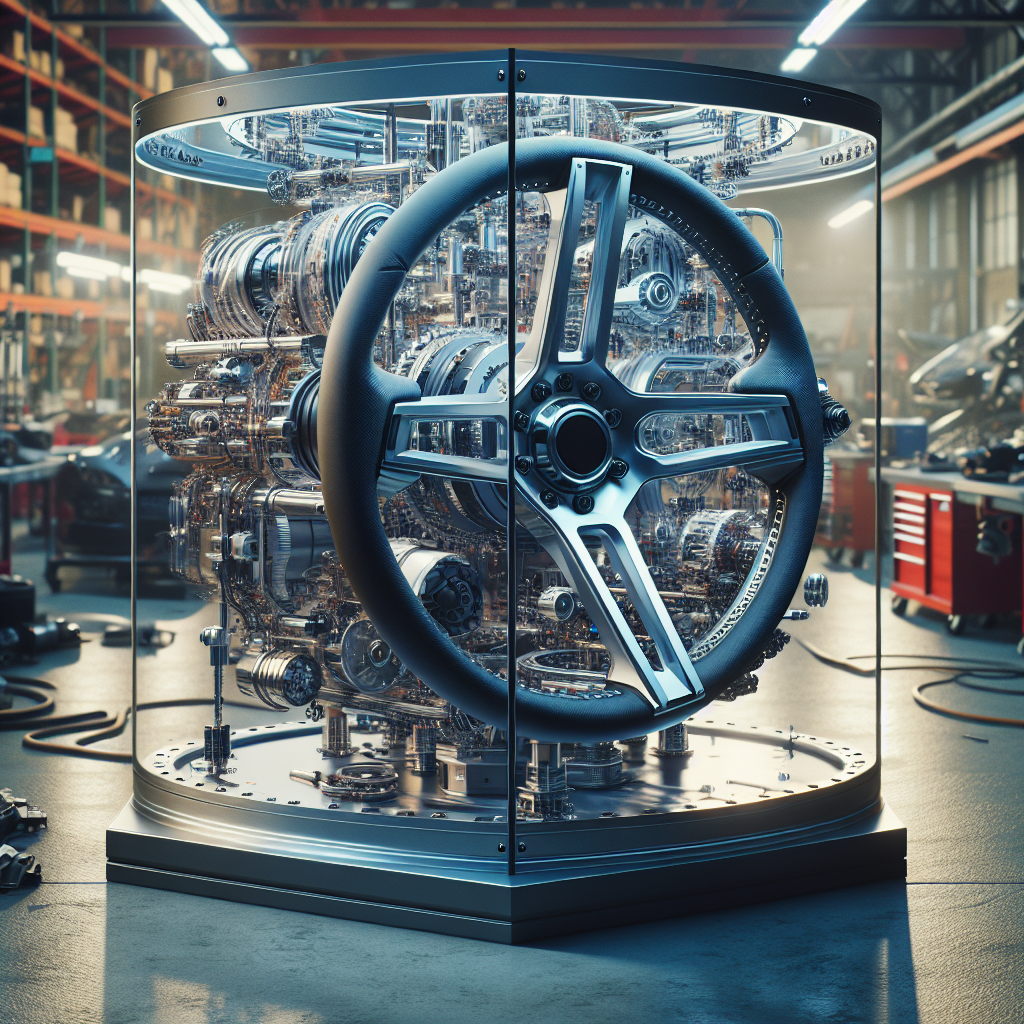
1. Plastic Wheel Simulators
Plastic is one of the most common materials used in wheel simulators, primarily due to its cost-effectiveness and versatility. High-density polyethylene (HDPE) and acrylonitrile butadiene styrene (ABS) are the go-to plastics for this application. HDPE is known for its strength and resistance to impact, while ABS provides a smooth finish that can easily be painted or coated for a polished look.
Pros:
- Lightweight, reducing the overall weight on your vehicle.
- Easy to install and remove.
- Available in a variety of colors and finishes.
- Generally more affordable than metal options.
Cons:
- May not be as resistant to high temperatures
- Can fade or become brittle over time with prolonged exposure to sunlight.
2. Aluminum Wheel Simulators
Aluminum offers a step up from plastic, providing a more durable and robust option. Aluminum wheel simulators are typically crafted from die-cast aluminum, which allows for intricate designs while maintaining a lightweight profile. These simulators are often polished or anodized for a shiny finish, making them an attractive choice for those looking to enhance their vehicle's aesthetics.
Pros:
- Higher durability compared to plastic.
- More resistant to extreme temperatures and impacts.
- Sleek finish that holds up better against UV rays.
Cons:
- Typically more expensive than plastic options.
- May require more maintenance to maintain appearance over time.
3. Stainless Steel Wheel Simulators
For those looking to combine strength and style, stainless steel wheel simulators are an excellent choice. These simulators are often made from polished stainless steel, offering a shiny, mirror-like finish that is resistant to rust and corrosion.
Pros:
- Extremely durable and resistant to harsh weather conditions.
- Attractive finish that enhances the look of any vehicle.
- Long lifespan with minimal maintenance needed.
Cons:
- Heavier than plastic or aluminum, which can impact vehicle performance slightly.
- Higher price point compared to other materials.
4. Chromed Wheel Simulators
Chromed wheel simulators are made from a base material (often plastic or metal) that is coated with a layer of chrome. This option offers the ultimate in shine and elegance, simulating the look of chrome rims without the substantial cost.
Pros:
- Dramatic appearance that mimics high-end chrome wheels.
- Corrosion-resistant, especially if made from metal.
- Easy to clean and maintain.
Cons:
- Chromed surfaces can be prone to scratches and chipping.
- May require specific cleaning products to avoid damage to the chrome finish.
Conclusion
Choosing the right material for your wheel simulators can significantly affect the overall look and longevity of your vehicle's wheels. From lightweight plastic to robust stainless steel, each material has its advantages and disadvantages depending on your specific needs and budget.
At [Your Company Name], we have been the premier supplier of hubcaps, wheel covers, and wheel simulators since 1979. We take pride in offering a wide range of products that cater to every vehicle owner's style and performance needs. If you need more information or assistance in selecting the perfect wheel simulator for your vehicle, our team is here to help!
Transform your vehicle with the right wheel simulator today!